EtherCAT’s Impact on PLCopen Standard
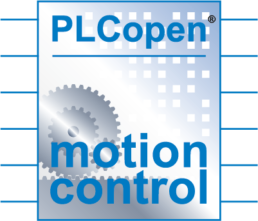
Overview
EtherCAT technology has had a significant impact on the PLCopen standard by providing a high-speed, real-time communication protocol that can be used in industrial automation applications. PLCopenhas developed guidelines for programming EtherCAT networks and integrating EtherCAT devices into PLC systems. EtherCAT’sability to improve system performance and reduce costs has led to its increasing adoption in industrial automation, and PLCopen’s guidelines help ensure that EtherCAT-based systems are reliable, interoperable, and maintainable.
And most importantly, combining EtherCAT and PLCopenstandards creates a powerful machine automation and integration environment because they create a plug-n-play platform that supports a mixed vendor (e.g. Servo drives). As an example, www.KINGSTAR.com for more details.
Benefits
- High-speed, real-time communication for industrial automation applications
- Reduced system costs and increased performance
- Improved interoperability between different devices and systems
- Consistent, standardized approach to programming & design of EtherCAT systems
- Easy maintenance and troubleshooting of EtherCAT-based systems due to clear guidelines and best practices provided by PLCopen standard.
Key Features
A PLC (Programmable Logic Controller) with EtherCAT (Ethernet for Control Automation Technology) utilizes Ethernet-based communication to transmit control signals between the PLC and other devices such as sensors, actuators, and other controllers.
Some key features of a PLC with EtherCAT include:
- High-speed communication: EtherCAT provides fast communication between devices at rates up to 1000 times faster than traditional fieldbuses, allowing for real-time control and monitoring of processes.
- Flexible topology: EtherCAT is a flexible topology, meaning that devices can be daisy-chained or connected in a star or tree configuration, allowing for greater scalability and easier integration with existing systems.
- Deterministic control: EtherCAT provides deterministic control, which means that data transmission and processing are synchronized to a clock, ensuring precise timing and coordination of multiple devices.
- Reduced wiring and installation costs: EtherCAT reduces wiring and installation costs by allowing devices to be connected in series, reducing the amount of cabling required and simplifying installation.
- Easy integration: PLCs with EtherCATare easy to integrate with other systems and devices, and can communicate with other networks such as Modbus and CANopen, making it ideal for use in a variety of industrial applications.
Overall, PLCs with EtherCAT offered a high-performance, flexible, and the most cost-effective solution for industrial automation and control.